We got to know Dücker Prefeeder BV during our Pilot Project with Emba when commissioning the first 295 QS Ultima. During the preparation stage for this project, we were well advised and helped by Dücker Prefeeder BV. Good advice from knowledgeable people with years of experience in the industry who manufacture the Prefeeder themselves. The fact that the Prefeeder comes from our beautiful Kempen region is a nice bonus. After a smooth installation and commissioning, we have now been in production for a year without any problems. Meanwhile, together with Dücker Prefeeder BV, we are looking for new possibilities to increase output on other machines in our facilities.
OUR HISTORY
Dücker Prefeeder BV was founded 2015, in the footsteps of Metlas Metaalindustrie BV and Meulendijks Solutions BV. Metlas Metaalindustrie has been a well known supplier of steel construction and laser-cut products for almost 30 years.Metlas Metaalindustrie has engineered, produced, manufactured and serviced Prefeeders for Serco-Holland untill 2000, from then on for Alliance Machine Systems Europe untill they decided to take production and manufacture to eastern countries. Metlas has always been a key engineering partner in the development of AMSE Prefeeders. Meulendijks Solutions is a well known specialist in world wide corrugated pheripherals with its base in the Serco-Holland organisation, which dates back to 1990. Among other products, prefeeder R&D has always been a key activity as well as upgrading and maintaining existing machines. The result was a vast knowledge of older types Prefeeders (which we still service and maintain) as well as about the newer Prefeeder types RMF and Linefeed. As it turned out, both RMF and Linefeed were not fit to carry the Prefeeder business into the future, therefore we developped our DPF (Block-push-Prefeeder) and DLF (Linefeed Prefeeder) from scratch, keeping the good aspects and finding state-of-art solutions for many areas of concern. All this resulted in 2 series of machines which are fully capable of meeting today‘s corrugated packaging demands, in terms of line speed, capacity volumes as well as parts used and manufacturing repeatability..
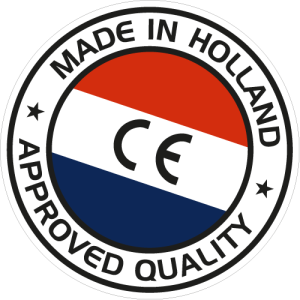
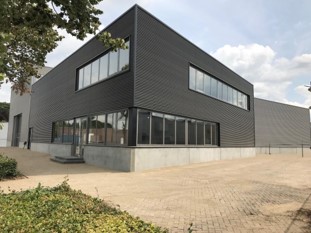